Energy Storage for IoT
Author: Ed Spence
9/5/2023
Abstract
A survey and comparison of low capacity and rechargeable energy storage technologies applicable to low power wireless sensor applications.
Introduction
There is extensive literature available regarding the use of batteries and other energy storage devices focused on large energy storage for EVs and backup power applications. Relatively little is written about energy storage for IoT applications, or how the various technologies might be applied to increase the operating life of energy storage in wireless sensor applications.In this series of articles we will discuss small capacity energy storage technologies that may be applied in wireless sensors, the various technologies available, their characteristics and how they can be leveraged to extend the operating life of a wireless sensor.
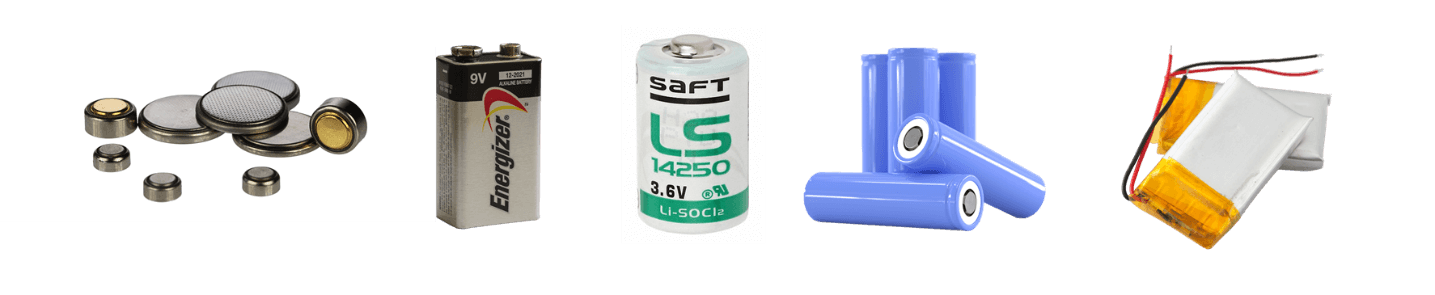
Figure 1. A selection of battery technologies, left to right a) Coin cell, lithium manganese dioxide chemistries (Li-MnO2), b) Alkaline, replaceable batteries commonly used for consumer applications, c) Lithium Thionyl Chloride (Li-SOCl2), a high density technology with a flat discharge voltage often found in wireless sensors and d) Lithium Ion (Li-Ion), e) Lithium Polymer (Li-Po) both are high capacity rechargeable technologies that can be manufactured in various sizes and shapes, hence likely used in your mobile device.
Batteries store electrical charge chemically within an electrolyte, or substances that allow ions to flow between anode and cathode. The electro-chemical construction of various battery technologies also determines the fully charged voltage and energy storage capacity of the battery.
Battery capacity is defined by the amount of steady state current that the battery can deliver at 25 °C before the voltage drops below a pre-defined usable level (or on a single charge, if rechargeable), typically defined as the Cut-off voltage. Battery vendors typically specify charge capacity (in A-Hr) associated with a nominal average discharge current, providing voltage as a function of discharge time.
Various battery technologies have been developed to deliver a variety of charge voltage levels, charge capacity (size), energy density (chemistry and manufacturing), recharge capability and form factors, each suited for different applications.
Supercapacitor based devices broaden the energy storage device category by storing charge between electrode plates electrostatically. These devices are optimized to deliver power to a load in a short time e.g. behaving like capacitors.
Hybrid Supercapacitors (also known as Lithium-Ion Capacitors) mix battery technology with supercapacitor construction, trying to optimize the power delivery with charge storage capacity, such that these devices will also be included in this discussion.
To complete the survey, we should point to a relatively recent addition to Lithium based variations, Lithium Titanate Oxide, or LTO. This technology delivers much higher Cycle Life than other lithium technologies with lower self leakage. Products available today cite 25,000 charge/discharge cycles and self-discharge less than 5%, performance associated with Supercapacitors. This ‘hybrid’ battery technology provides modest capacity like a battery, though has lower energy density than other lithium technologies.
A partial list of energy storage technologies1 available today are shown in Table 1.
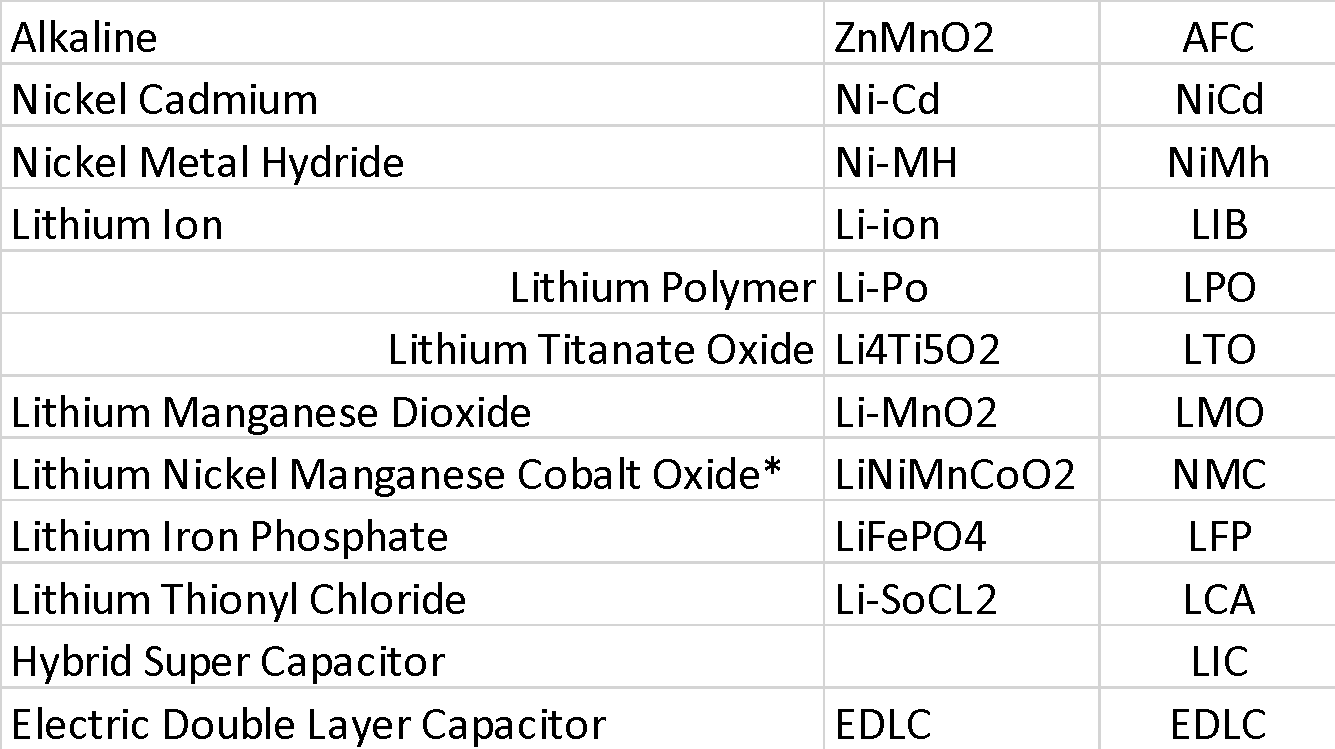
Table 1. Energy storage technology chemistries and commonly used short hand acronyms.
Energy storage technologies can be characterized first by their fundamental energy storage characteristics, such as fully charged Voltage and Energy Density (Watt-hours) as a function of battery volume or weight, the former more useful for portable applications and the latter more critical for mobile applications such as drones or EVs.An important distinction to make with regard to energy capacity is the ability to deliver that energy over a period of time (e.g. power). The technologies described above are designed to either store energy for the long term, delivering it in smaller measures over a longer period of time (energy) or to deliver energy (power) very quickly when needed with less ability to provide long term capacity, or some trade off of both characteristics. A graphical depiction of the energy delivery capabilities of the three classes of energy storage technologies is shown in Figure 22.
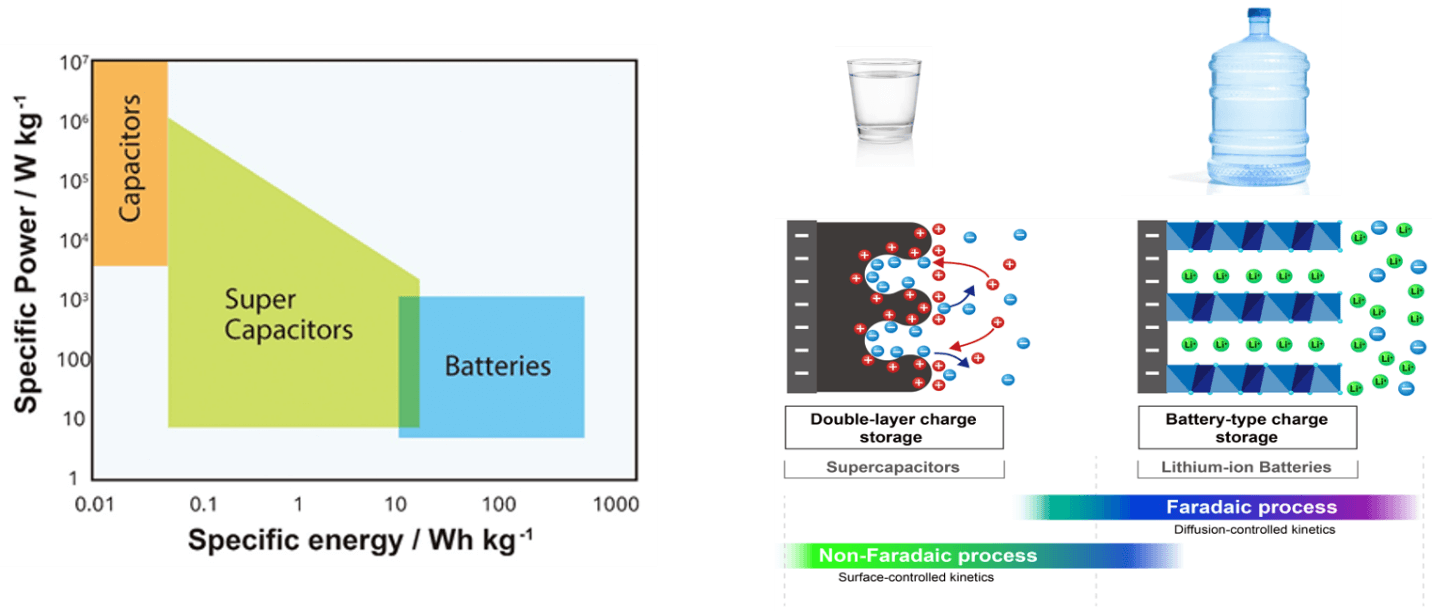
Figure 2. Energy delivery differences between electrostatic, hybrid technology and chemical charge storage with ability to deliver the charge to a load is likened to storage and delivery of water from different types of containers. Image courtesy of Nichicon Corporation.
Energy Storage Figures of Merit
Capacity
Battery capacity is defined by the amount of steady state current that the battery can deliver at 25 °C before the voltage drops below a pre-defined useable voltage level (or on a single charge, if rechargeable).
Capacity is primarily determined by chemical composition and size of the battery, but for a given battery model capacity will also vary greatly depending on how it is used (average current consumption) and by environmental factors such as temperature of operation. The ambient operating temperature may be the primary determinant of battery performance available from any specific battery model, followed by the features and performance of the application in which it is used.
Note that battery capacity is generally stated as ‘nominal’, specified with an average current draw, cut-off voltage, and operating temperature.
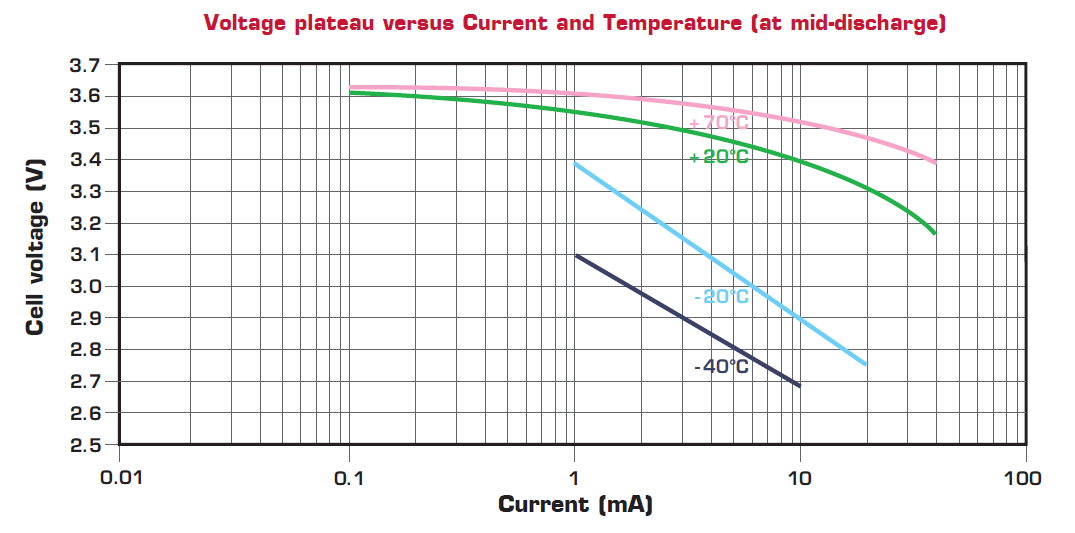
Figure 3. Battery performance curves showing heavy dependency of capacity on both temperature and average current drawn from the battery. This graph is from the datasheet of a 3.6 V, 1,200 mAh LS14250 ½ AA Li-SOCl2 battery (Image Credit: Saft Batteries).
Energy Capacity and Cycle Life
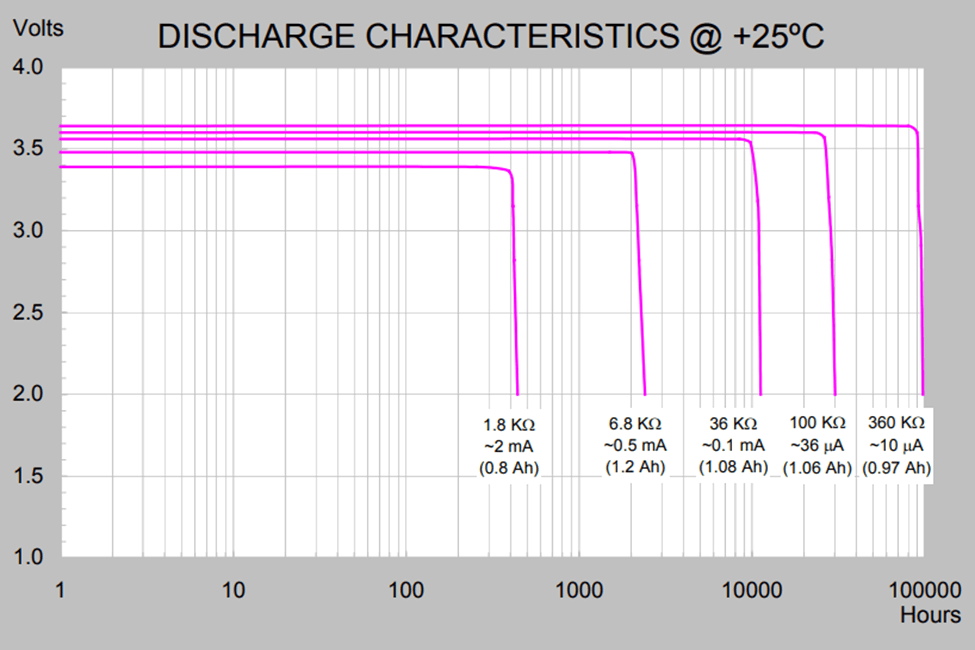
Figure 4. Battery discharge characteristics determine the battery capacity. Operating life supported by the capacity of a specific battery model will vary with the average current consumed by the application. Users can estimate battery life by interpolating between provided curves for an average current closest to their application (Image credit: Tadiran), though this estimate can vary greatly depending on the application and environmental conditions.
Though common to discuss ‘battery life’ in the context of an IoT application, it would be more technically accurate to refer to Energy capacity of an energy storage device, which is can be related to operational lifetime as a point in time (hours) where the open circuit voltage (OCV) level available at the battery terminals drops below a particular level, known as the voltage cut-off. Testing is a complicated process as a specific average current draw must be maintained while the internal battery resistance changes. In a simplified model, an average current is drawn from a fully charged battery by applying a load periodically to the battery representing an average current draw. The duty cycle is such that the battery chemistry has time to ‘rest’ when not loaded, allowing the battery output to revert to the Open Circuit voltage (OCV). Testing is time consuming, inversely proportional to the average current for the test, making testing a challenge for low current applications such as IoT or wearable applications3.
For rechargeable energy storage, even more important that nominal capacity in terms of operational life is the Cycle Life. Expressed as a number of charge / discharge cycles, Cycle Life is typically cited with 80% of capacity used each cycle, known as the Depth of Discharge, or DOD.
Note that for rechargeable technologies Cycle Life and DOD effectively determine the operational life of the device. For most lithium based technologies, the number of cycles over the life of the device can be maximized by minimizing DOD to less then 80%. Note that this restriction is not relevant to Supercapacitor technology and less relevant to hybrid technology or LTO batteries, which can repeatedly deliver all of their stored charge without impacting overall capacity available for each cycle.
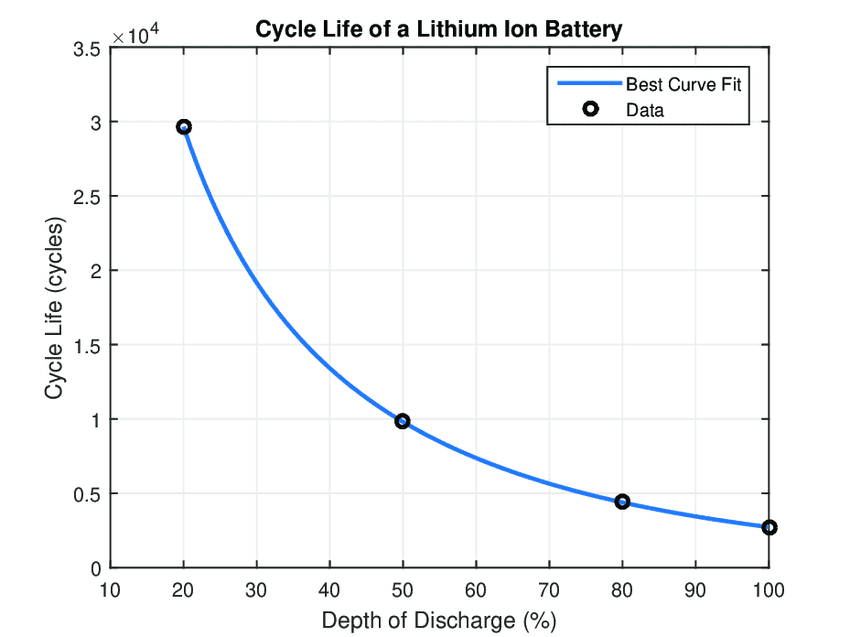
Figure 5. Figure showing the relationship between DOD and Cycle Life. Image credit: ResearchGate.net, Creative Commons4
Charge / Discharge Characteristics
Rechargeable batteries offer the promise of longer lifetime before disposing of the battery, a solution that offers both economical and environmental benefits. But this capability can be confused by the different charge and discharge characteristics of the various battery technologies. Environmental factors and application variables that impact battery capacity also influence the rate, efficiency and overall number of charge/discharge cycles that a battery will deliver during its useful life.
For example, discharging or charging a battery too fast (charge current too high) may damage the electrodes and increase the internal resistance. The discharge or charge rate is typically specified as a fraction of the overall capacity, C. Charging at the nominal rated capacity implies a 1 hour charge rate. Charging at a lower rate, for example C/2, implies a 2 hour time frame and so on.
Figure 6. The charge time of a 150 mAh LTO battery, as a function of charge current. Note that 1 C is equivalent to 150 mA. Courtesy Nichicon Corporation.
The rate of charge is also key to safely using any battery technology. The chemical process of moving charge from one electrode to another has limited efficiency due to internal resistance of the material, producing heat as a byproduct. Charging or discharging some battery technologies too quickly can cause mechanical swelling due to excess heat, leakage, internal damage, and even combustion of the battery. Maximum charge currents cited in the device specifications should be well understood when designing the power management circuitry for any application.
Finally slower rates minimize capacity degradation, whereas faster rates of charge reduce the usable voltage and degrade the total capacity. Degradation of capacity is exacerbated by the number of cycles and DOD as well (see Figure 7. This characteristic makes minimum and maximum charge current (proportional to time to charge) figures of merit for rechargeable batteries5.
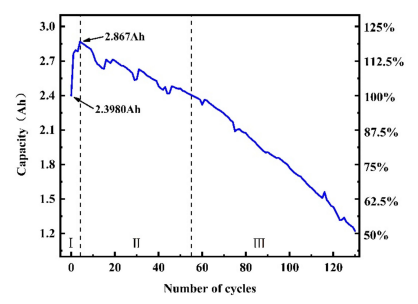
Figure 7. The discharge capacity changes of a type NCM811 battery during 130 cycles at the cycle ratio of 2 C with the cut-off voltage of 1 V6.
Intelligent charging or power management circuitry for the application will typically monitor Voc, temperature and occasionally current flow (Coulomb Counter) in order to efficiently and safely charge any battery technology. This circuitry is often integrated into the battery package.
That said, Supercapacitors or LTO technology can be charged with constant voltage (CV) profiles and hence simpler power management circuitry such as LDO or DC-DC converter.
Self-discharge (Leakage)
An important characteristic of any battery technology, and refers to the tendency to lose charge while in transport or storage. Rates of leakage vary with technology and conditions, but in general accelerates at elevated temperatures due to residual reactions within the chemistry. Leakage is generally more pronounced soon after achieving a full charge, with the rate slowing over time.
Type | Self-discharge |
Nickel–cadmium battery(NiCd) | +++ |
Nickel–metal hydride battery(NiMH) | ++++ |
Lithium Cobalt Oxide (LCO) | +++++ |
Lithium Manganese Oxide(LMO) | +++++ |
Lithium Nickel Manganese Cobalt Oxide(NMC) | +++++ |
Lithium Iron Phosphate(LFP) | +++++ |
Lithium Titanate(LTO) | +++++ |
Lithium polymer battery(LiPo) | +++++ |
Electric Double Layer Capacitor(EDLC) Super Capacitor | + |
Lithium Ion Capacitor(LIC) Hybrid Super Capacitor | +++++ |
Table 2. Relative self-discharge performance of various energy storage technologies.
Operating Temperature Range
The performance of all batteries is severely degraded at low temperatures. Charging conventional lithium-ion batteries at sub-zero temperatures is dangerous due to potential for dendrite formation (internal short circuits). Standard lithium-ion batteries have higher resistances, so operation at extremely low temperatures can result in overcharge/over-discharge voltages, leading to thermal runaway resulting in ruptures or even combustion. For this reason some designs contain thermistors within battery packs to prevent low-temperature operation. Some battery technologies can perform at a lower temperature range than others, with LFP, LTC, and LTO batteries specifying the lowest sub-zero temperature range.
Energy Storage Technologies – Comparisons in a Bit More Detail
Alkaline (ZnMnO2)
Alkaline batteries are a one use battery technology with a 1.5 V nominal voltage. This technology is widely used for applications that consume current in limited amounts but at a steady rate (such as flashlights). The lowest energy density of the technologies reviewed here, the voltage and capacity decay steadily with use, making battery life estimates easier than with other technologies, which have a less linear response.
Nickel Cadmium (Ni-Cd)
The discharge characteristics of Nickel-based battery technologies, Cadmium and metal-hydride are very similar, with open circuit voltages (OCV) of 1.25 V to 1.35 V, nominal voltage of 1.2 V (per cell) and cut-off voltage of 1.0 V. That said, Ni-Cd has a lower capacity and more rapidly degrading discharge voltage than the newer Ni-MH technology.
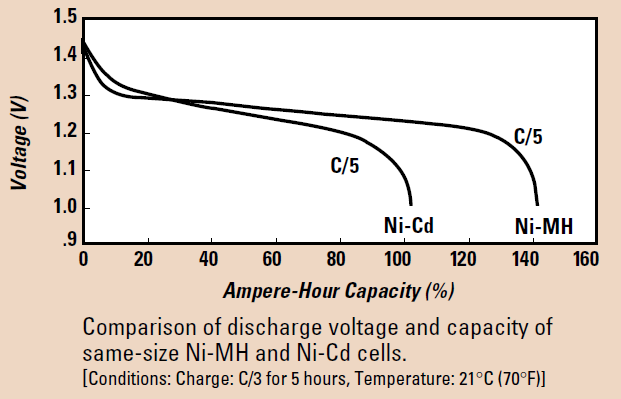
Figure 8. A comparison of Ni-MH and Ni-Cd technologies, nominal output voltage with respect to Capacity at the same discharge rate. Note charge conditions for time and temperature cited (image credit: Duracell Ni-MH Technical Bulletin, downloaded August 2022)
To prevent overcharging a Nickel-based cell, the Voc is monitored to detect a slight drop in voltage as full capacity is reached. The Voc is monitored by the charging circuitry, which switches to a slower ‘trickle’ charge to bring the cell to 100% charge. Charging circuits are ‘constant current’ output circuits rather than using a voltage threshold for this reason.
Nickel based technology is sensitive to repeated charge and discharge cycles without complete discharge, where upon the cell will ‘remember’ a partial discharge, also known as Voltage Depression or memory effect6. Partial discharge leaves active materials that have not been cycled leaving an increase in internal resistance. The effect on battery performance is for both capacity and discharge voltage to reduce with each discharge cycle. In Ni-MH technology, full capacity can be restored with a few complete discharge cycles (that is, complete discharge to 1.0 V).
Ni-Cd batteries have been largely replaced by Ni-MH technology, due to improved performance and to eliminate use of Cadmium which is considered toxic.
Nickel Metal Hydride (Ni-MH)
Ni-MH cells are a popular rechargeable replacement for Alkaline batteries in high current consumption (high drain) applications such as digital cameras, where they outperform on a single charge, maintaining relatively flat voltage until discharged beyond usable charge capacity. For this reason, some portable applications will be designed to use the nominal 1.2 V of the Ni-MH rather than a 1.5 V Alkaline alternative.
Charging circuits are typically ‘constant current’ output circuits rather than using a voltage threshold due to the non-linear behavior of the internal resistance and also since Voc is one of the battery characteristics monitored to detect a full charge. The most common charging method is to detect a slight drop in Voc at full charge, calibrated for temperature. Efficiency for constant current charging is typically 66%, degrading with faster charge times. One charge equipment vendor recommends charging a Ni-MH battery overnight at C/10 (13 hours to 15 hours). At 20 C, even overcharging may warm the battery slightly but not cause damage7.
A fully charged Ni-MH cell might deliver up to 1.25 V during discharge, declining to 1.0 V per cell, after which permanent damage to the cell chemistry may occur, particularly when multiple cells are used in the same application. Damage due to polarity reversal, where one or more cells discharges before the others due to differences in manufacturing tolerances, causing the cells still containing charge to drive the under charged cells. This phenomena, like overall battery behavior, is temperature dependent.
Self-discharge (leakage) of Ni-MH cells, although better than the earlier Ni-Cd technology, can be as high as 5% to 20% of capacity on the first day of use before stabilizing anywhere from 0.5% to 4% per year at room temperature. This self-discharge rate increases dramatically with temperature, with Duracell recommending storage at 10 °C to 30 °C when not in use.
Optimum performance for Ni-MH cells occurs between 0 °C and 45 °C. Performance suffers modestly at higher temperatures, but degrades more rapidly at lower temperatures.
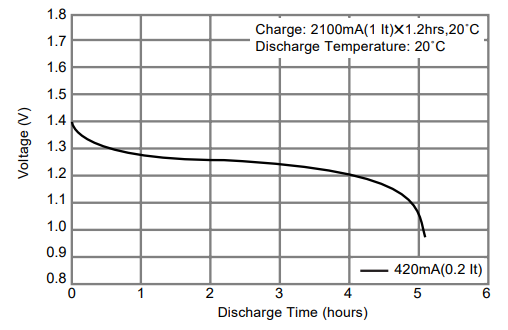
Figure 9. Datasheet discharge curve for the Panasonic 1.2 V A size HHR210A 2,100 mAh rated Ni-MH.
Lithium Ion (Li-Ion)
This technology was developed during the 70’s, with the first patent assigned to Exxon in 1977. Continued development through the 80’s had to overcome safety issues due to short circuits caused by dendrite formation in the lithium metal anodes. Technology with an intercalation anode to prevent these formations was commercialized by a Sony / Asaji Kasei team in 1991. Improvements in energy density and safety have been made since then, with Li-Ion batteries adopted for a wide variety of applications, from portable electronics to EVs8. Global Lithium-ion battery production capacity has grown from 20 GWh in 2010 to 767 GWh in 2020, with China accounting for 75%9.
A lithium ion (Li-ion) battery contains a cathode and anode both of which can be made from compounds of lithium atoms. The electrolyte is made of lithium salt in an organic solvent. Both electrodes allow lithium ions to move in and out of their structures with a process called insertion (intercalation) or extraction (deintercalation). Because lithium ions move back and forth between the two electrodes, this battery technology has been called ‘rocking-chair’ or ‘swing’ battery technology.
Lithium based batteries outperform Nickel based technologies in many respects - the overall life cycle is much longer, they charge faster, hold their capacity over a broader temperature range, have lower self-discharge rates (1.5% to 2% per month) and have a higher charge voltage (3.6 V). Li-Ion batteries also do not suffer from charge ‘memory’ effects.
On the other hand, NiMH technologies are generally lower cost, are more environmentally friendly and are free from transportation regulations that apply to Li-Ion when shipped.
The biggest shortcoming of Li-Ion technology is in regard to safety. Many variations of the technology can overheat if not charged carefully, and can be damaged when overcharged, leading to thermal runaway and combustion. Several high profile fires and recalls over the years have driven research activity to make Li-ion technology safer to use, but also given rise to regulation regarding storage and transport. Embedded safety features have also been added to limit voltage and reduce internal pressures, at an increase in cost.
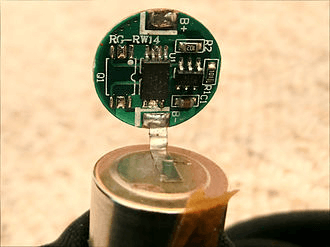
Figure 10. Integrated charge management circuitry for a Li-Ion battery. Image credit: GeoTab.
Charging is accomplished in two stages, the first by applying a constant current (much like NiMH), but then transitioning to a constant voltage phase (trickle charge). Charging temperature limitations are more limited than operating temperature. The chemistry performs well at elevated temperatures but excessive operation at higher temperatures reduces battery life. Vendors recommend charging at a lower temperature range (typically 5 °C to 45 °C) to maximize battery life but the result is often slower (longer) charge times. Charging at sub-freezing temperatures damages the battery, which cannot be recovered by cycling.
Degradation of Li-Ion capacity to store energy or deliver power over time is a well researched topic given the wide spread use of Li-ion technology in EVs. Although power degradation is a natural process, the conditions under which this process is accelerated or retarded is of great interest to automotive manufacturers. Tools have been developed from EV usage to help users understand how to better manage battery life dependencies on usage variables such as time, temperature, operating state of charge (SOC), current consumption and charge/discharge cycles. In one study, it was found that battery systems operated at higher temperatures (ie no cooling systems) and frequent high power charging impacted battery life more than age or number of charge/discharge cycles10. This data is very relevant to EV driver demands for shorter charge cycles.
Finally, Lithium based electrolytes enable the battery to be constructed and formed into a variety of shapes to fit the application, making it a popular choice for mobiles, EVs, laptops, drones, consumer wearables, medical devices, power tools and other products positioned by form factor and industrial design, and requiring high energy density.
Research continues for Lithium based cells to increase energy density, optimize power delivery, and to increase safety. Many variations on Lithium based electrodes and electrolytes have been brought to market, each creating trade-offs in terms of performance, safety, etc.
Lithium Polymer (Li-Po)
Polymer electrolytes were developed to help prevent the formation of dendrites in lithium, in order to prevent short circuits11. Lithium-ion batteries use liquid as the electrolyte, limiting the flexibility of the shape and hence packaging. A method was devised to use conductive polymers in the form of a gel instead of liquids to create a layered film, which can be made smaller, lighter, and thinner. Lithium polymer batteries have a higher energy density (about 1.5 times that of a lithium-ion battery of the same volume) and are hence smaller than lithium-ion batteries of the same energy density.
Li-Po is a safe technology. Even if a short circuit occurs, it often results only in gas emission. They do not burn easily, and use less toxic substances than lithium-ion batteries. The disadvantage is that lithium polymer batteries are more expensive.
Lithium Manganese Dioxide (Li-MnO2)
The Lithium Manganese oxide battery features long-term reliability, having a life span of 10 years with low leakage current. This technology is widely used in electricity, gas and water meters, fire and smoke alarms, security devices, backup batteries and RTC power in portable devices. Coin cell Li-MnO2 batteries are rechargeable.
Lithium Thionyl Chloride (Li-SOCl2)
Li-based batteries with Thionyl Chloride (SOCl2) cathodes seems to be a material of choice for IoT devices for industrial applications, such as vibration based condition monitoring, where sensor sizes can be constrained, transducer technologies may benefit from higher supply voltages, high energy density is beneficial, and wide operating temperature ranges are required. High cost, safety concerns and the highly toxic nature of the cathodes requires special disposal procedures. This technology is not rechargeable.
Lithium Titanate Oxide (Li-TiO2, or LTO)
LTO technology occupies a unique position in the energy storage universe, straddling the performance space between Lithium-ion and Electric Double Layer Capacitors (EDLC). LTO can deliver a higher power discharge than typical Lithium–ion and for a longer period of time than a Supercapacitor, due to generally higher energy density and less leakage. Capable of a very high number of charge/discharge cycles, LTO has a longer service life than Li-ion but shorter than capacitors.
A lithium-titanate battery uses lithium-titanate nanocrystals, instead of carbon, on the surface of its anode. This increases the anode service area by approximately 30x compared to carbon, allowing lithium ions to enter and leave the anode quickly. Li-Ti cells are capable of fast charging (higher charging current, up to 20 C) which is much safer since lithium dendrites are less likely to form. Lithium-titanate cells available today last anywhere from 3,000 to 25,000 charge cycles.
Like capacitors, LTO technology can also be charged with very low trickle charge currents, making it a good charge storage companion for energy harvesting or scavenging systems.
A disadvantage of lithium-titanate batteries is their lower charge voltage (2.4 V), compared to 3.7 V for conventional lithium-ion battery technologies. For today’s low voltage electronics and sensor technologies this is not necessarily a limitation for circuit designers.
Supercapacitor (Electric Double Layer Capacitor or EDLC)
Supercapacitors are specialized energy storage devices, distinct from most battery technologies in several important ways. As capacitors, EDLC technology is well suited for rapid transfer of power, with virtually unlimited ability to charge and discharge with little loss of performance, whereas battery technology stores energy for longer term use.
According to Eaton Batteries12,
In a battery, the act of recharging is inherently faradaic. It involves forcing the ions at the cathode electrode back to the anode to a point where there is sufficient electrochemical potential. However, the charge and discharge processes usually necessitate an irreversible interconversion of the chemical electrode reagents or ingredients. The cyclic stresses on the battery lead to the cracking of the electrode material and the decomposition of both the solvent and salt components of the electrolyte, which eventually prevents any reversible electrochemical reactions. Li-ion batteries form a permeable passivation layer called the solid-electrolyte interphase (SEI) on the electrode surface. This allows for blocks of electrons to pass while also preventing the electrolyte decomposition, therefore, extending the cycle life. However, this SEI formation and growth also consumes active Li and electrolyte materials, causing a reduction in capacity and power density. Another aging mechanism is the breakdown of the SEI layer, which leads to overheating and immediate failure.
Hybrid Supercapacitor
So called Hybrid Supercapacitors as the name implies are a mix of both supercapacitor and battery technologies, in that the electrode construction enables enhanced charge storage on the electrodes instead of chemical stored at the junction with the electrolyte13. The differences in the three technologies in terms of construction and ability to deliver power are shown graphically below.
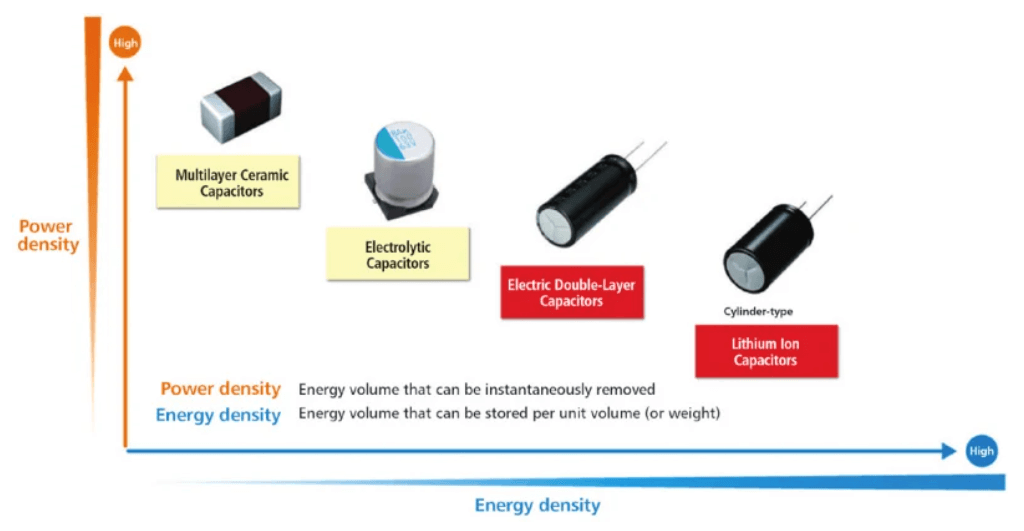
Figure 11. Graphical positioning of energy storage technologies with respect to power vs energy density. Image credit: Taiyo Yuden Tech Briefs, June 2021
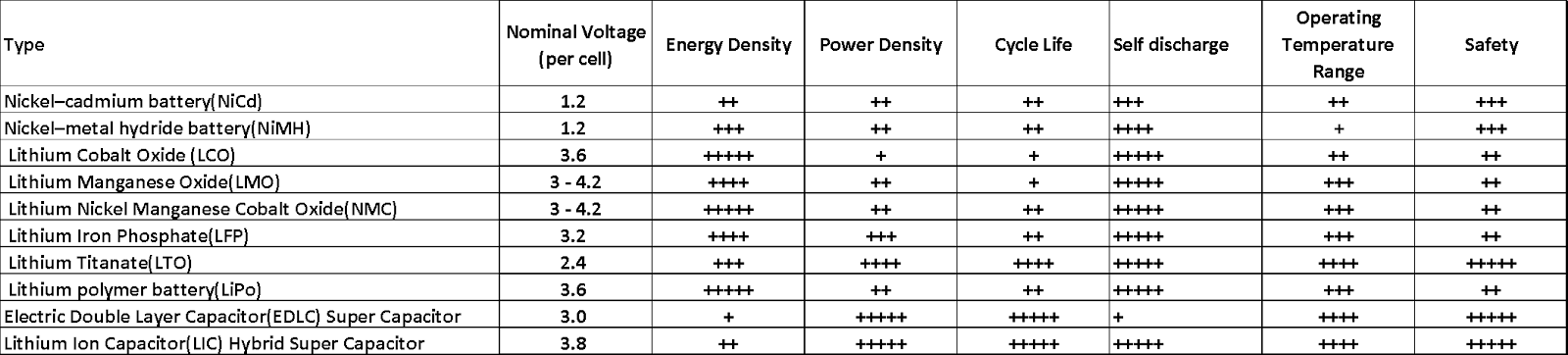
Table 3. Comparison of Figures-of-Merit for Representative Energy Storage Devices
Summary
Considering the complex nature of energy storage and the wide variety of technologies and products available on the market today, the following factors need to be taken into consideration to narrow the choices for IoT applications:
- The lowest voltage at which the device circuitry can operate.
- Operating temperature range of the device.
- Total operating duration of the device expected for the application.
- The number of times the battery may be discharged and recharged over the operating life.
- Whether the battery function is primarily to provide steady energy over longer time periods or short duration power.
- Measurement and transmission intervals, or the duty cycle of operational states versus sleep mode.
- The maximum amount of time required for charging.
- The cut-off voltage of the battery.
- Physical dimensions of the device that needs to incorporate the battery.
- Environmental and electromagnetic characteristics that will affect battery life directly or indirectly.
- Overall cost of ownership (CAPEX vs OPEX).
About the Author
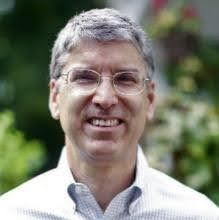
Ed Spence is the Founder and Managing Director of The Machine Instrumentation Group, a collaborative network of contract engineering service providers with an available pool of over 150 hardware, software and mechanical engineers.
Our broad array of technical competencies includes a deep working knowledge of machine health which includes IoT system and software development, vibration sensor technology and design, vibration measurement and signal processing, and data engineering for predictive maintenance.
1 Acronyms and abbreviations associated with energy storage can be found on the Battery University web site.
2 A helpful infographic on this subject from Saft Batteries can be found here.
3 Estimating battery life in an actual application is a much more complicated endeavor, as current draw profiles for an application such as an IoT sensor add additional layers of complexity due to the device operating states, circuit design and power management, radio transmission protocol efficiency and operating environment in addition to battery technology and capacity.
4 “Electric vehicles as means of energy storage”, Ameli et al, Energy Storage in Energy Markets, 2021
5 “Effect of High-Rate Cycle Aging and Over-Discharge on NCM811 (LiNi0.8Co0.1Mn0.1O2) Batteries”, Yin et al, MDPI Energies Journal, April 2022
6 This is not to be confused with normal capacity loss with aging, which can be accelerated by over-charging, or storage or use at high temperatures.
7 PowerStream BLOG, June 6, 2022.
8 Li-Ion technology is used in the Nissan Leaf and the Tesla Model S. For comparison, gasoline has approximately 100x more energy density at 12,700 Wh/kg or 8760 wh/L. Clean Energy Institute, University of Washington.
9 Murray, Cameron (8 March 2022). "Europe and US will shave c.10% off China's Li-ion production capacity market share by 2030". Energy Storage News
10 "New Data Shows Heat & Fast-Charging Responsible For More Battery Degradation Than Age Or Mileage". CleanTechnica. 16 December 2019
11 Girishkumar, G.; McCloskey, B.; Luntz, A. C.; Swanson, S.; Wilcke, W. (2 July 2010). "Lithium−Air Battery: Promise and Challenges". The Journal of Physical Chemistry Letters.
12 Eaton Battery vs Supercapacitor Whitepaper, February 2022
13 Note that in a capacitor no charge is stored in the dielectric between charge plates, but on one plate or the other.